Solutions
Electrostatic Dissipative (ESD)
In facilities with sensitive electrical equipment, such as clean rooms, data centers, and pharmaceutical labs, static control flooring is a must. Static electricity is generated when a person walks across a floor then comes in contact with an object. While it takes about 3,500 volts for someone to feel any sensation from the electricity being transferred, it only takes about 25 volts for static shock to damage sensitive equipment.
Our electrostatic dissipative coating systems disperse electricity and prevent shock to people and equipment – all while giving you the aesthetics and performance benefits of a resinous floor.
Dissipative needs vary based on static levels and the type of equipment being utilized within your space. Give us a call; we can help identify the right solution for your environment.
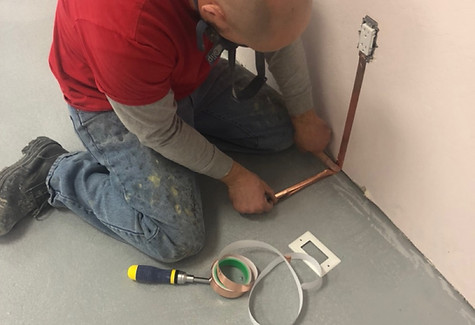
We can evaluate your facility and customize a system that's designed meet your specific flooring needs.
System Overview

01
Concrete Prep & Patching
We begin by industrial diamond grinding the concrete to a CSP 3 surface profile, ensuring optimal conditions for maximum epoxy mechanical bonding. This meticulous surface preparation is crucial for the long-term durability of the ESD epoxy system. We employ Terrco industrial grinders, renowned for their superior performance and industry-leading quality.
02
100% Solids Epoxy
Next, a layer of 100% Solids Pigmented Epoxy is then applied to the prepped concrete. This base coat provides a solid, durable foundation for the subsequent layers, ensuring excellent adhesion and mechanical strength.
03
100% Solids Epoxy
After the base coat has cured, a build coat of 100% solids epoxy is applied to further enhance the floor's durability and thickness. This layer is mixed and applied similarly to the base coat, ensuring an even and consistent coverage. The build coat is crucial for achieving the desired floor thickness and providing additional strength and resilience to withstand heavy traffic and mechanical stress. It also helps to fill in any minor imperfections in the base coat, creating a smoother surface for the top coat. The build coat is then allowed to cure fully.
04
Grounding Copper Strip
Next, a grounding copper strip is installed. This strip bridges the gap between different flooring types, providing a continuous path for static electricity to dissipate safely to ground, thereby protecting sensitive electronic equipment and enhancing overall safety in environments where electrostatic discharge is a concern.
05
ESD Conductive Urethane
The final step in the ESD epoxy system is applying a top coat of ESD conductive urethane. This specialized coating is designed to provide electrostatic dissipation, making it essential for environments where static control is critical. Once applied, it is allowed to cure, completing the ESD epoxy flooring system and delivering a durable, static-controlled, and aesthetically appealing floor.
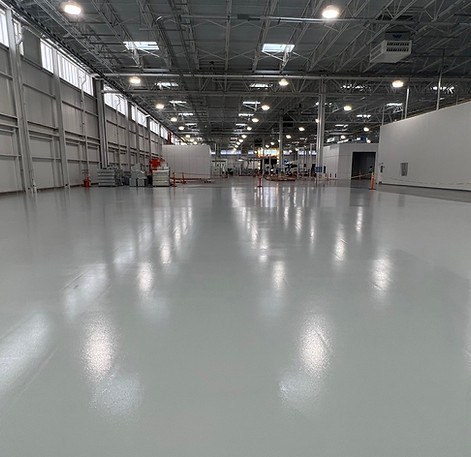
Nikola
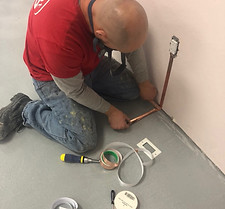
ESD Installation

Boeing Apache Helicopter
SYSTEM CHARACTERISTICS
EFFECTIVE ELECTROSTATIC DISSIPATION
The primary benefit of an ESD epoxy flooring system is its ability to provide effective electrostatic dissipation. This property is crucial in environments where static electricity can damage sensitive electronic equipment or pose safety risks. By grounding static charges, the ESD epoxy floor helps prevent electrostatic discharge incidents, ensuring the safe operation of electronic devices and protecting valuable components. This makes it an ideal flooring solution for data centers, electronics manufacturing facilities, and other high-tech environments.
DURABILITY & STRENGTH
An ESD epoxy flooring system is highly durable and strong, thanks to its multiple layers of 100% solids epoxy. These layers create a robust surface that can withstand heavy foot traffic, machinery, and equipment without cracking or deteriorating. The system's strength ensures long-lasting performance, reducing the need for frequent repairs or replacements. This durability makes it suitable for industrial and commercial settings where the floor must endure significant wear and tear over time.
CHEMICAL RESISTANT
The top coat of ESD conductive urethane adds significant chemical resistance and UV stability to the flooring system. This protection means that the floor can resist damage from spills of harsh chemicals, oils, and solvents, making it easy to clean and maintain. Additionally, the UV stability of the top coat prevents the floor from yellowing or degrading when exposed to sunlight, ensuring that it retains its appearance and integrity for years, even in environments with substantial light exposure.
EASY MAINTENANCE
The seamless and smooth finish of the ESD epoxy flooring system simplifies cleaning and maintenance. Without seams or joints where dirt and bacteria can accumulate, the floor is easy to sweep, mop, and disinfect, promoting a hygienic environment. This benefit is particularly important in settings such as laboratories, clean rooms, and healthcare facilities, where cleanliness and hygiene are paramount. The low-maintenance nature of the floor also reduces the time and cost associated with upkeep.
Portfolio
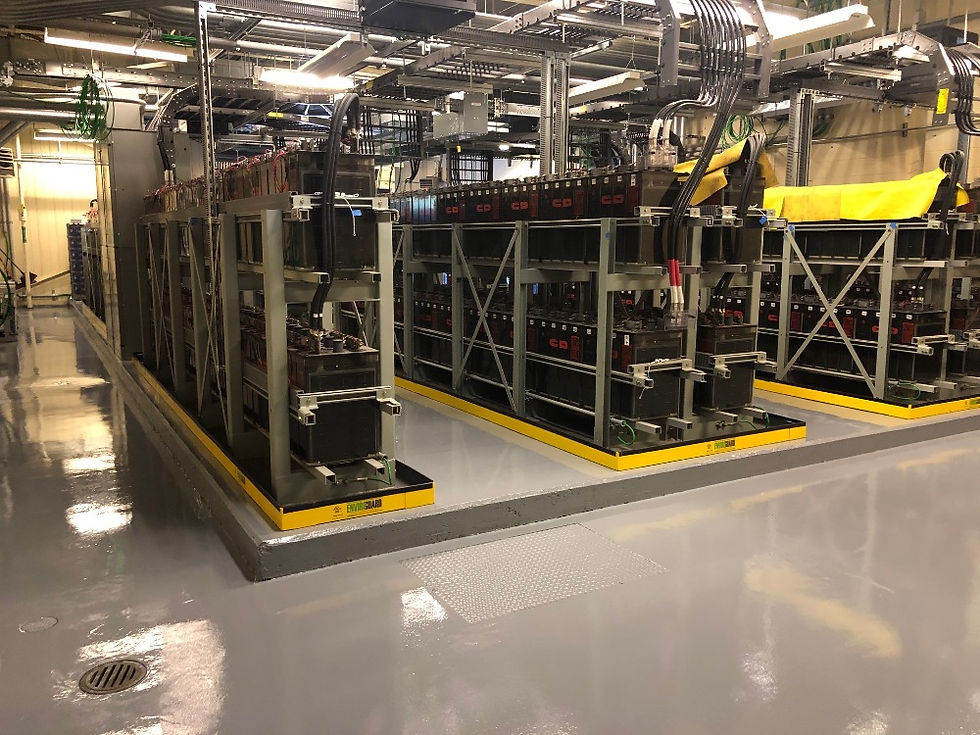


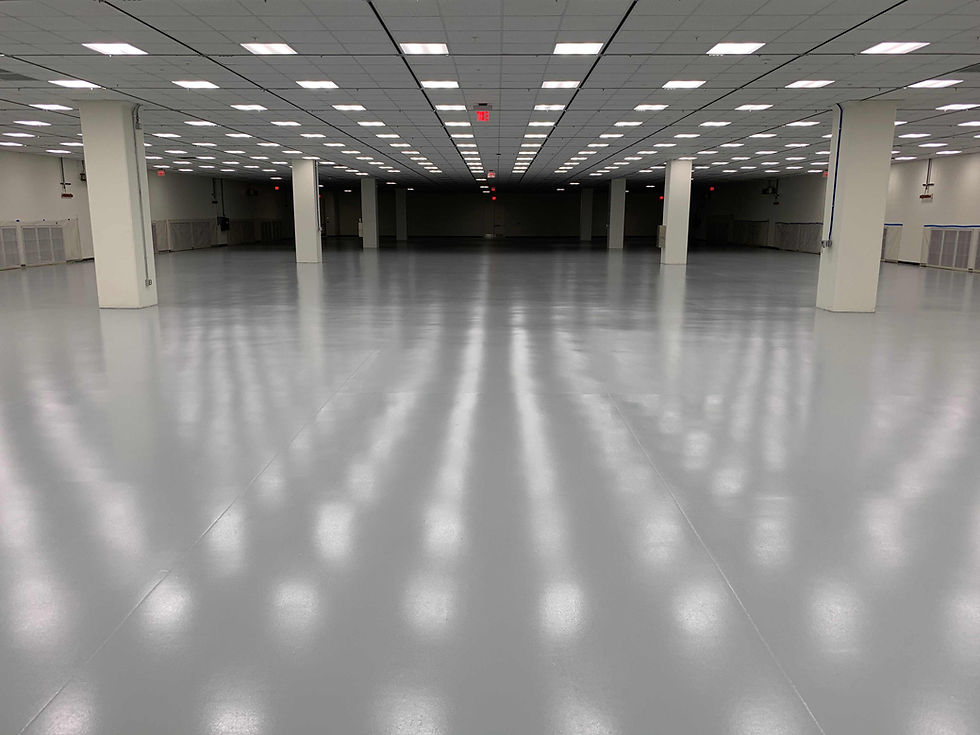
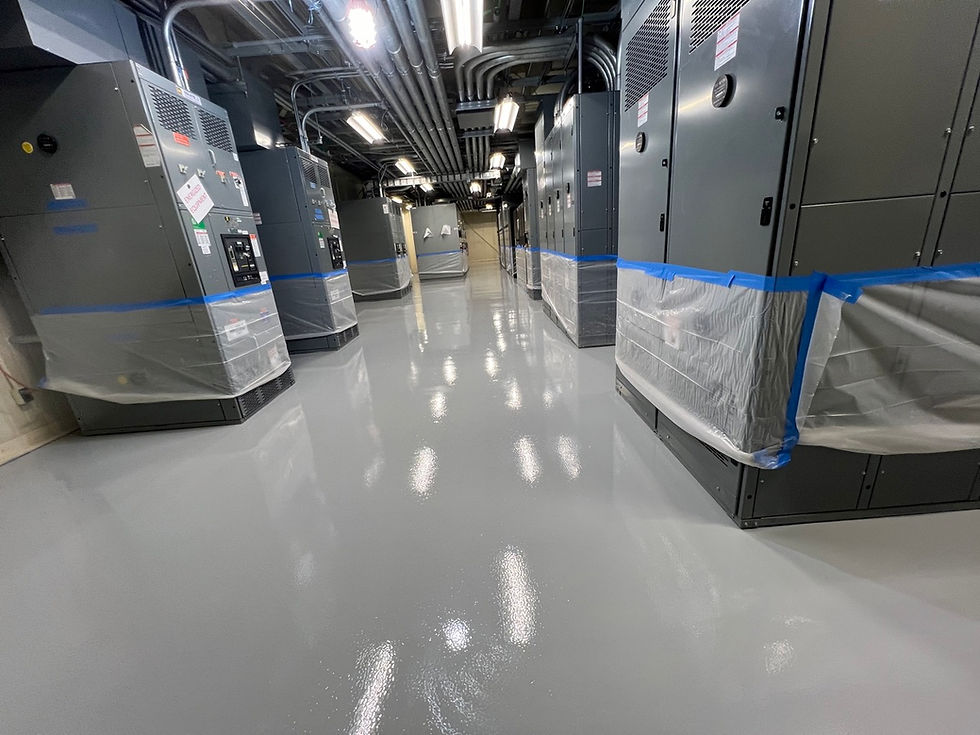

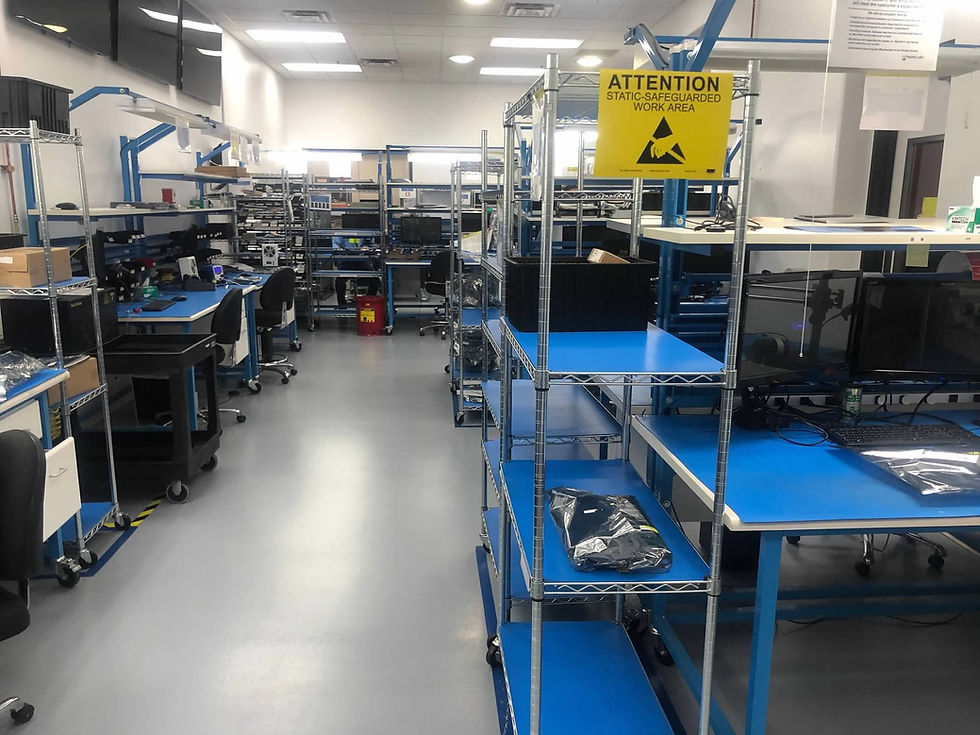
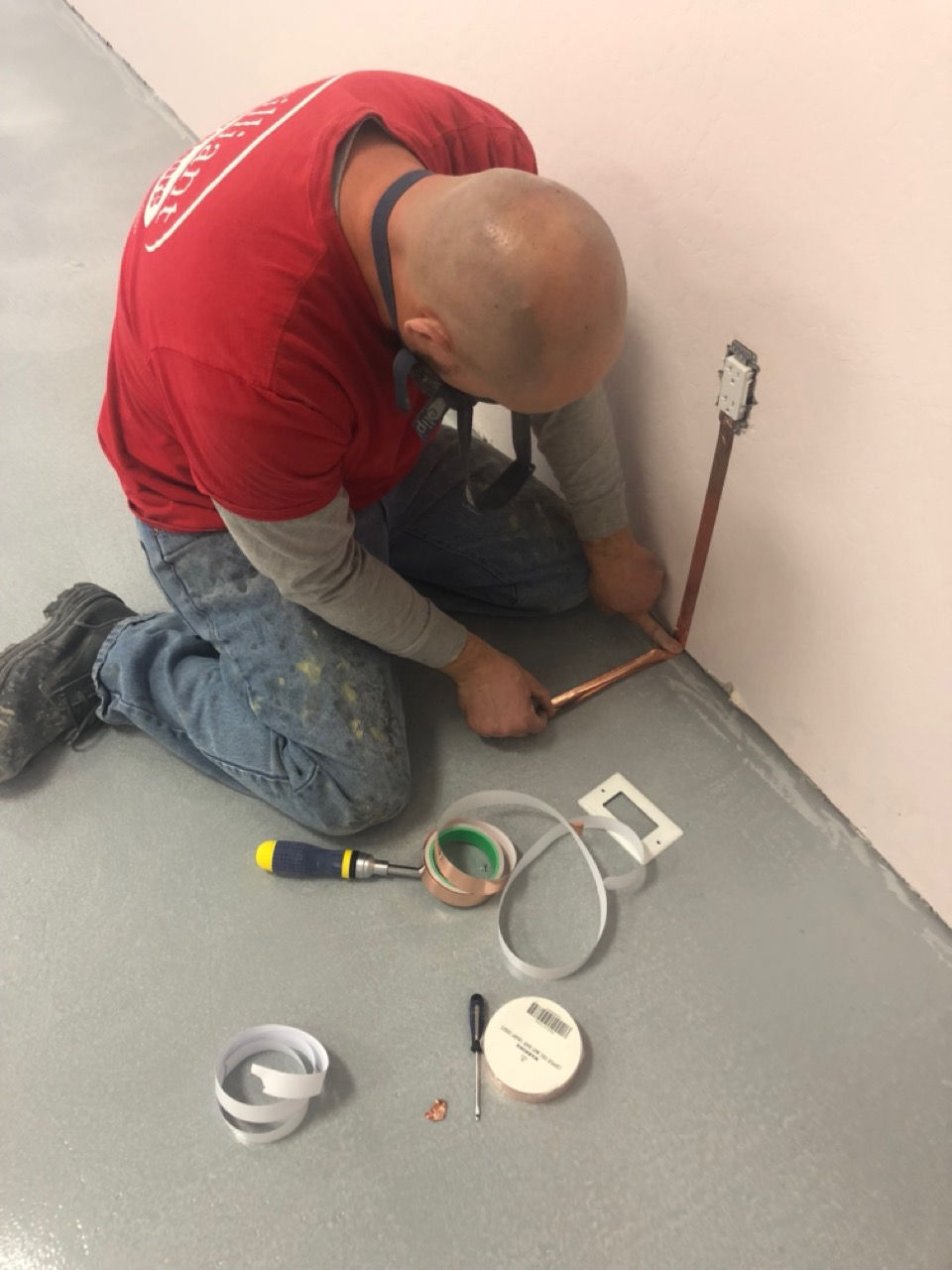
